Will 2021 be a remake, reborn, or a remix for the industrial manufacturing sector? The answer depends on which consulting agency you ask.
At Edvantis, we’d rather settle for a confident, technology-driven restart. The ongoing pandemic may have distracted certain plans and forced some companies to pivot rapidly. Most importantly, it forced many manufacturing leaders to re-evaluate their current tech stack and accelerate digitization.
The Manufacturing Market Outlook for 2021
Understandably, the global pandemic cast a heavy toll on the industrial sectors. Ongoing
supply chain disruptions, production stop-starts, and emerging regulatory demands for adapting the workflows were among the several stressors manufacturing leaders had to deal with throughout the year.
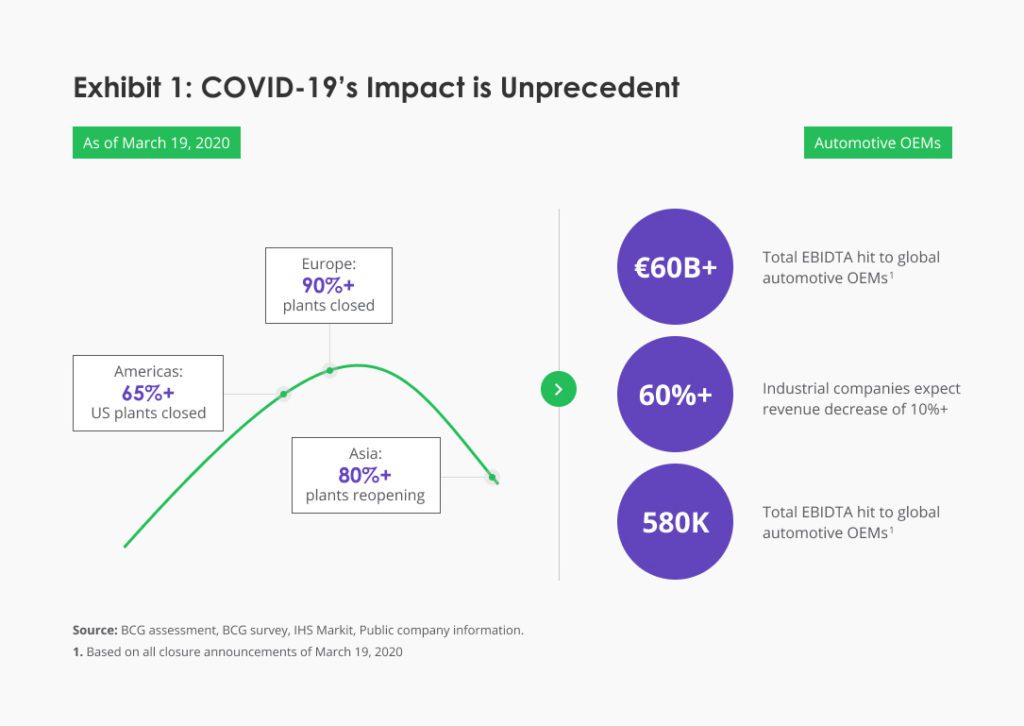
Source: BCG
In 2021, operational matters still remain complex and economic uncertainty remains a “given”. But there’s room for optimism too. An early market outlook from McKinsey indicates that 52% of manufacturing leaders expect a full recovery in the next 6-24 months.
EY prognosis is more tempered. Among their respondents, 53% expect a “U-shaped” recovery with the dip extending well into 2021.
How industrial manufacturing (IM) leaders are gearing up for the recovery? According to a PwC survey, CEOs are taking the following actions in response to the pandemic:
- 34% plan to increase reliance on artificial intelligence
- 37% expect to explore predictive maintenance
- 43% also treat the pandemic as an opportunity to modernize their enterprise resource planning (ERP) systems
Not so surprisingly, McKinsey data also revealed that 56% of manufacturers who have not implemented Industry 4.0 technologies — the cloud, industrial IoT, process automation solutions, and advanced analytics — before the pandemic ended up being more constrained in their response to the pandemic.
Indeed, IT manufacturing solutions have proven to be crucial for weathering the storm. As we enter the recovery phase, investment in new technology will also be determinant for improving operational performance, containing costs, and diversifying into new revenue streams.
6 Dominant Technology Trends in the Industrial Manufacturing Industry
Despite, or more likely because of a taxing year, industrial leaders are actively exploring new technology industry trends and did not cut down on technology spending. On the contrary, many are actively investing in new industrial and systems engineering solutions, factory automation solutions, and legacy systems modernization.
Based on our discussions with clients and internal analysis, we found that the following technology investments will have a strong impact on the business recovery prospects:
1. Industrial IoT
Industrial Internet of Things (IIoT) technology is hardly novel. Since the mid-2010s, leaders in the IM space have been testing different use cases, ranging from asset management to smart meters and wearable devices for employees.
Airbus upgraded its premises to the “Factory of the Future” — a connected, digitized manufacturing environment that relies on intelligent, connected production tools to streamline repetitive tasks, reduce error rates, and enhance quality control. Siemens, Bosh, and GE are among other poster projects in the space.
In 2021, the industrial IoT market keeps growing. Gartner predicts that by 2028 over 1.9 billion IoT units will be installed in the manufacturing and natural resources industries. The figure is 5 times higher compared to 2018.
That’s the big picture, however. When it comes to actual progress, the adoption figures are more modest. Data from 2018 suggests that only 15% of IIoT initiatives were successfully scaled within a year. A quarter of them stayed in pilot mode for two years, and nearly half never made it past the test stage.
What this data telling us is this: Industrial IoT deployments, especially large scale, are large and complex. The sensor devices themselves are highly affordable and relatively easy to program. But larger-scale deployments require technological maturity and data science expertise.
Before considering IIoT adoption make sure that:
- Your current architecture can support IoT devices
- Legacy systems and applications are capable of supplying or accepting data from IoTs. If not, consider refactoring critical apps as microservices and distributing them as open APIs
- Map which functions (e.g. warehousing, asset management, logistics) will benefit the most from new technology investments
- Determine the optimal target deployment environments for new technologies — edge, on-site, or cloud.
- Ensure that your IT and operational technology (OT) investments are well-aligned.
2. PLC Programming
Programmable logic controllers (PLC) are not a new technology industry trend either. But the growing demand for complex process automation and industrial equipment programming across the factory floors heats up the PLC marker.
Between 2021 and 2027, the USA, Canada, Japan, China, and Europe will drive a 4.3% CAGR for this market. Globally, the PLC market is predicted to reach $16.9 Billion by 2027.
Thanks to its affordability and multi-purpose capabilities, PLCs remain in active use across industrial sectors — from oil and gas construction to HVAC management — to establish real-time control systems for an array of machinery.
PLCs are the cornerstone of industrial automation. It’s not giving away its position in 2021, despite the growing interest in IIoT devices, which support more complex automation scenarios thanks to better sensing capabilities.
3. HMI Development
Operators on the floors demand more convenient interfaces for operating complex machinery. So it follows that leaders are considering better HMI (human-machine interface) solutions for industrial manufacturing.
By 2027, the global HMI market is projected to grow to $8,77 billion with technologies including artificial intelligence and IoT fostering the growth of this market.
HMI terminals enable more convenient, safe, and cost-effective communication between the machine and the operator, providing timely alerts, operational guidance, and easy programming experience for connected systems such as I/O and PLC applications. So that instead of calling an Industrial Engineering Specialist, operators can fine-tune machinery performance or an entire system using graphical, user-friendly interfaces and controllers.
HMI SCADA solutions, in particular, are growing in demand. Given the rapid rate of digitization across factory flows, most operators now demand more consolidated interfaces for centrally monitoring all the equipment performance, exercising control, or tuning the settings. Many operations now require remote monitoring. HMI/SCADA solutions provide your teams with web-based interfaces and mobile apps for controlling the operations at a distance. Such setup leads to significant operational advantages.
Case in point: Subaru recently adopted a new HMI/SCADA solution, providing the Ops teams with real-time plant-wide monitoring and control capabilities. Post-adoption the auto manufacturer achieved a 98.6% trim shop uptime and a 300% increase in production volume over 12 years.
If your organization is considering HMI development for SCADA (plans to integrate a proprietary solution), consider the following factors:
- Interoperability. Is it possible to integrate the new software and hardware units with all existing equipment? What types of refactoring/customizations will be required?
- Security. How will you handle network security and data encryption? What security facets the solution provides (e.g. strong authentication)?
- Updates. Does the vendor provide regular software and firmware updates? If not, who will be responsible for maintenance?
4. Predictive Maintenance
Predictive maintenance is another ongoing technology trend in the manufacturing sector. That makes sense given that the average hourly cost of operational downtime is still estimated at six digits: between $100,000 to $300,000, depending on the industry.
Predictive analytics solutions, configured to estimate the timing of equipment breakdowns, have already proven to drive substantial ROI.
A predictive maintenance program can help achieve a 70% reduction in equipment breakdowns, 35%-45% reduction in downtime, and 25%-30% reduction in maintenance costs. Cumulatively, all of the above can yield a tenfold increase in ROI for industrial manufacturers.
US Department of Energy
Some of the common predictive analytics solutions use cases in manufacturing include:
- Asset condition monitoring
- Root cause failure analysis
- Just-in-time servicing
- Improved spare parts ordering
But as with other technology investments, predictive maintenance requires a certain level of operational and data management maturity. In particular, to build accurate predictive algorithms you need to be able to track the correct parameters and have timely access to operational data. IIoT devices and PLC apps both can act as robust sources for analytics and enable you to run different simulations and gauge accurate predictions.
5. Advanced performance analytics
Classical industrial engineering focused on maximizing the efficiency of individual workers and machines. A greater degree of digitization and connectivity now allows IM leaders to get a more holistic picture of the entire operational ecosystem, featuring complex relationships between the people, processes, machines, and smart devices.
By applying data science to performance data you can identify overlooked optimization opportunities, underperforming assets and processes, as well as obtain new insights for decision-making.
The two primary use cases of data science include:
Self-service descriptive analytics. Such algorithms assist with data interpretation, pattern detection, and interpretation of business rules applied to the data. It helps companies gain better visibility into ongoing and historical processes and understand why a certain event happened.
Descriptive analytics use cases in manufacturing:
- Production cycles evaluation
- Supply chain visibility analysis
- Benchmark performance data collection
- Equipment and asset performance data collection
- Equipment inspections and recalibrations
Predictive analytics. Predictive algorithms also rely on real-time and historical data to predict future outcomes, based on the identified relationships between different tracked variables. Such algorithms rely on time-series predictions, regression models, and other machine learning methods to estimate future outcomes.
Apart from predictive maintenance, predictive analytics use cases in manufacturing include:
- Demand forecasting
- Raw materials cost predictions
- Workforce performance management
- Warranty analysis
- Supply chain optimization
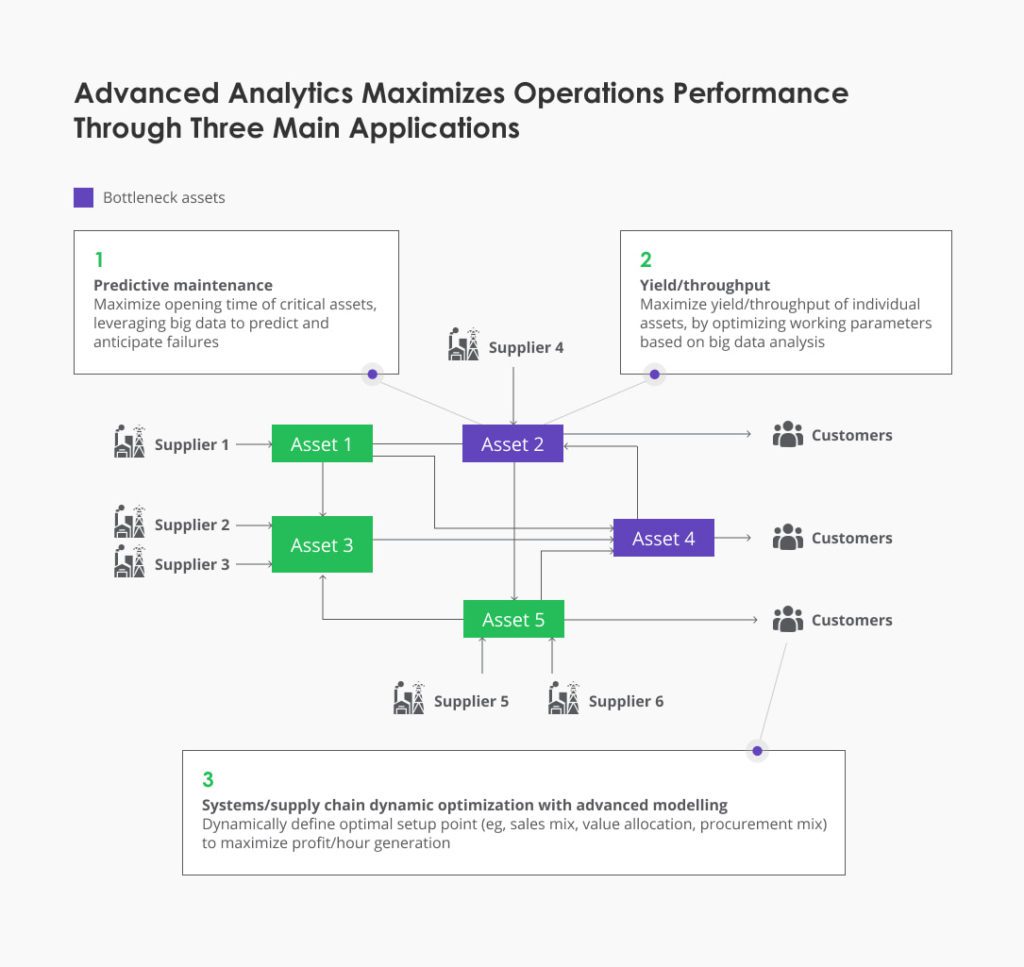
Source: McKinsey
6. Supply Chain Digitization
2020 gave the manufacturing industry a tough lesson in terms of supply chain resilience. In 2021, “resilience” remains a top-ranking priority for IM leaders. In fact, 39% of manufacturing companies plan to increase their investment in supply chain technology beyond the levels budgeted pre-pandemic.
Here’s how these budgets are spent:
- Integrated planning and execution: Prior to the virus outbreak, 84% of supply chain managers named “lack of end-to-end visibility” as their biggest challenge. Limited purview into up- and downstream data has led to ongoing waste and inefficiencies. So it follows that in 2021, many leaders are considering further improvements into supply chain visibility such as upgrades to ERP systems, adoption of integrated cloud platforms, centralized data storage repositories, and subsequent adoption of advanced analytics.
- Logistics visibility: Knowing how the inbound and outbound shipments move across the chain is crucial for improving production plans. By integrating “track and trace” data from vendor tracking systems into your supply chain management systems, you’d gain better planning precision.
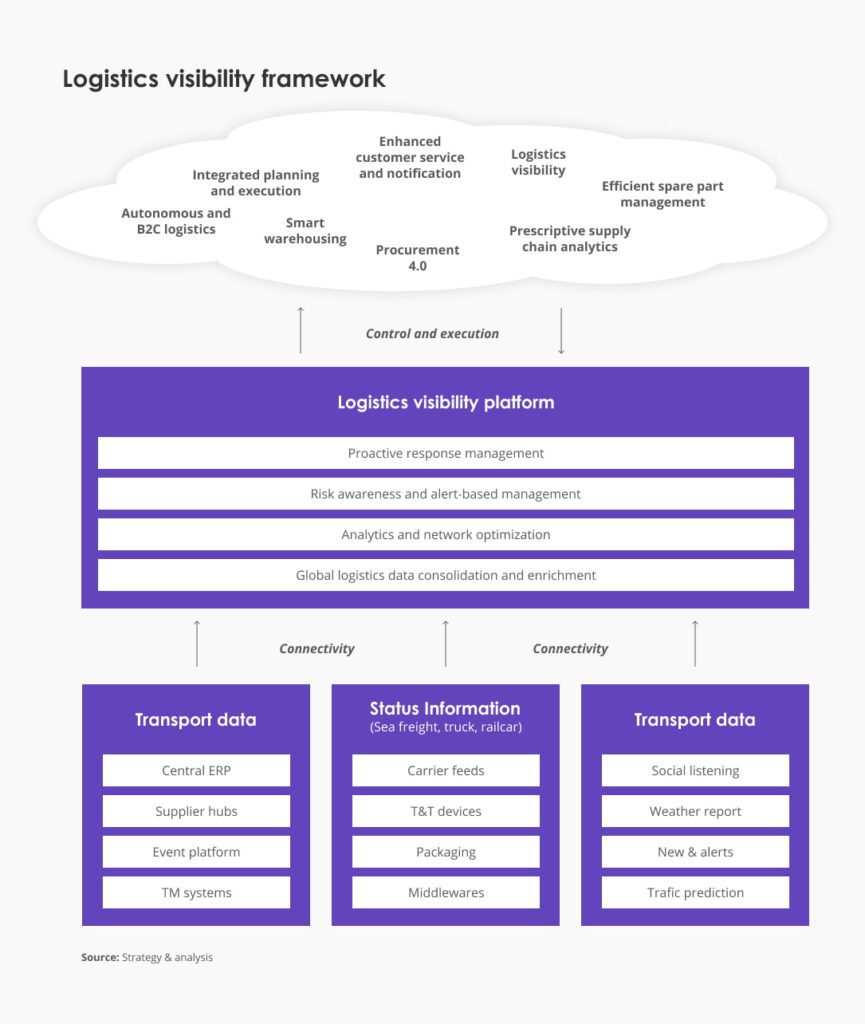
Source: PwC
- Enhanced procurement: Integrating your suppliers into your SCM system can facilitate collaboration, planning processes, sourcing, and risk management. By proactively sharing data and leveraging analytics tools for processing it, you can automate low-value repetitive tasks, speed up goods movement through the chain, and lower procurement costs.
What’s Ahead for the Industrial Manufacturing Sector
Last year gave the industry a solid shake-up. The global pandemic also inadvertently showed many leaders how emerging technologies can help maintain safe, secure, and effective operations at a distance — be in remote production management or collaboration with a new technology partner.
Cost containment will clearly remain an important priority. But there are different ways to achieve it with new technology investments being one of them. Process automation, ERP updates, predictive analytics solutions — all of the technology trends brought up on our list can help you get your operations in better shape.
Planning to upgrade your IT/OT systems? Learn more about our industrial engineering expertise. Or contact us directly if you have a specific question.